Share your thoughts, photos and general help to all builders
by JPXman » Thu Nov 02, 2006 9:58 am
-

JPXman
- LazairNUT
-
- Posts: 627
- Joined: Sun Nov 02, 2003 10:15 pm
by russell » Thu Nov 02, 2006 10:17 am
-
russell
- LazairNUT
-
- Posts: 366
- Joined: Wed Aug 10, 2005 1:39 pm
- Location: Valdosta, Georgia
-
by Shannon » Thu Nov 02, 2006 11:24 am
-
Shannon
- SHANNON
-
- Posts: 1084
- Joined: Thu Jan 15, 2004 10:05 pm
by russell » Thu Nov 02, 2006 12:29 pm
-
russell
- LazairNUT
-
- Posts: 366
- Joined: Wed Aug 10, 2005 1:39 pm
- Location: Valdosta, Georgia
-
by flyalaz » Thu Nov 02, 2006 1:29 pm
-
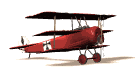
flyalaz
- LazairNUT
-
- Posts: 352
- Joined: Tue Sep 30, 2003 3:18 pm
- Location: Montreal, Canada
-
by Shannon » Thu Nov 02, 2006 5:08 pm
-
Shannon
- SHANNON
-
- Posts: 1084
- Joined: Thu Jan 15, 2004 10:05 pm
by Shannon » Thu Nov 02, 2006 11:53 pm
-
Shannon
- SHANNON
-
- Posts: 1084
- Joined: Thu Jan 15, 2004 10:05 pm
by russell » Fri Nov 03, 2006 8:15 am
-
russell
- LazairNUT
-
- Posts: 366
- Joined: Wed Aug 10, 2005 1:39 pm
- Location: Valdosta, Georgia
-
by JPXman » Fri Nov 03, 2006 10:38 am
-

JPXman
- LazairNUT
-
- Posts: 627
- Joined: Sun Nov 02, 2003 10:15 pm
by bdiedenhofen » Fri Nov 03, 2006 12:14 pm
-
bdiedenhofen
- Popular Lazair Member
-
- Posts: 65
- Joined: Sat Oct 11, 2003 7:55 pm
Return to Re-Building tips and info
Who is online
Users browsing this forum: No registered users and 576 guests